高灵敏压力传感器过载保护结构设计(2)
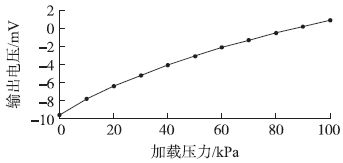
图3 压力芯片输出特性测试结果
由图3 可见,随着压力载荷的增加,输出电压并未随之线性增加,其增加的程度逐渐减小,而且满量程输出未达到设计要求。经过分析,出现图3 所示的现象应该是由于芯片的密封腔体有泄漏引起的。虽然有泄漏,但芯片仍然表现出了压力敏感特性,而且利用多晶硅纳米膜研制的硅杯结构压力传感器能够满足设计要求。因此,改善工艺解决泄漏问题后,牺牲层结构多晶硅纳米膜压力传感器的性能应该能满足设计要求。
2 牺牲层厚度对过载能力的影响
对于上述0.1 MPa 传感器,当最大应力达到硅的断裂强度4.5 × 108 N/m2 时,膜片底部与衬底不发生接触,过载能力不高。如果减小牺牲层厚度使膜片断裂前与衬底接触便可提高过载能力,牺牲层厚度越小过载能力越强,但不可避免会引入非线性形变,因此本文将利用静态线性分析与非线性接触分析相结合的方法,对牺牲层厚度进行优化设计,提高压力传感器的过载能力。
2.1 过载能力及极限过载能力
对于采用湿法腐蚀的扩散硅压力传感器,其压力敏感结构上的二氧化硅和氮化硅等绝缘或保护层厚度比弹性膜厚度小很多,一般在结构分析和应力分布分析中可以忽略它们的影响。但是,本文的牺牲层结构压力传感器的多晶硅弹性膜片厚度为3 μm、二氧化硅绝缘层厚度为0.5 μm,二氧化硅层厚度相对于多晶硅而言不可以忽略,所以在优化模拟仿真时需要考虑其对应力分布的影响。
利用有限元法对上述0. MPa 传感器的力敏结构进行模拟分析,可知当加载压力使膜片上的最大应力刚好达到硅的断裂强度时,膜片中心的挠度为1.6 μm。显然,牺牲层厚度H2 < 1.6 μm 时,膜片在断裂前可与衬底接触,因此,需要采用非线性接触分析来计算过载能力; 而牺牲层厚度H2≥1.6 μm 时,无需考虑膜片与衬底接触问题。
牺牲层厚度H2 < 1.6 μm 时,随着牺牲层厚度的减小,使膜片与衬底刚好接触所加载的压力也随之减小,当牺牲层厚度减小使该加载压力减小到刚好满量程压力时,牺牲层厚度不可再减小,否则传感器在量程范围内将出现了非线性形变,这样便确定了减小牺牲层厚度提高过载能力的极限值。经过仿真,膜片长度a = 300 μm、宽度b = 150 μm、膜片厚度H1 = 3 μm 时,对应的牺牲层厚度最小值为0.3μm。下面利用有限元分析软件对此参数的压力传感器进行非线性接触分析。按照模型建立、网格划分、接触对建立、加载、求解的顺序进行模拟仿真。当最大应力达到硅的断裂强度时,加载压力为1.55MPa,仿真结果如图4 所示,其中点O 处于膜片中心。
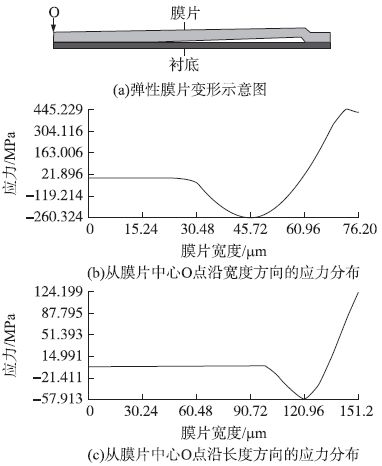
图4 四分之一弹性膜片极限变形剖面图
在压力传感器实际设计中,出于工艺精度的考虑,相比满量程加载时,牺牲层厚度的最小值应该留有余量。若以量程的50%为余量,则牺牲层厚度最小值应为加载0.15 MPa 时对应的尺寸。经过仿真后,留有余量的牺牲层厚度最小值为0.5 μm,此时当膜片最大应力达到硅的断裂强度时,加载压力为1.35 MPa。
牺牲层厚度H2 > 1.6 μm 时,进行线性分析仿真,以H2 = 3.5 μm 为例,按照模型建立、网格划分、加载、求解的顺序进行线性模拟仿真。当最大应力达到硅的断裂强度时,加载压力为0.47 MPa,其应力分布的仿真结果如图5 所示。
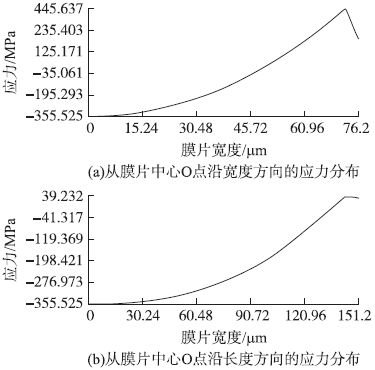
2.2 牺牲层厚度与过载能力间的关系
利用非线性接触分析与线性分析的仿真方法,对牺牲层厚度H2在0. 3 μm ~ 3. 5 μm 之间变化时进行具体的仿真,给出了膜片最大应力达到硅的断裂强度时,衬底和膜片之间的距离ΔH 与牺牲层厚度H2的关系,如图6 所示。同时也给出了膜片最大应力达到硅的断裂强度时所施加的压力载荷Pmax( 过载能力) 与牺牲层厚度H2关系,如图7 所示.
来看看其他人说了些什么?-----------------------------------------------------------------> 进入详细评论页